ASTANA — Kazakhstan is preparing for a public referendum to determine the location of its first nuclear power station. Many experts believe this move will pave the way for the development of nuclear energy in the country. If the public votes in favor of nuclear power construction, a critical question arises: where will the fuel come from?
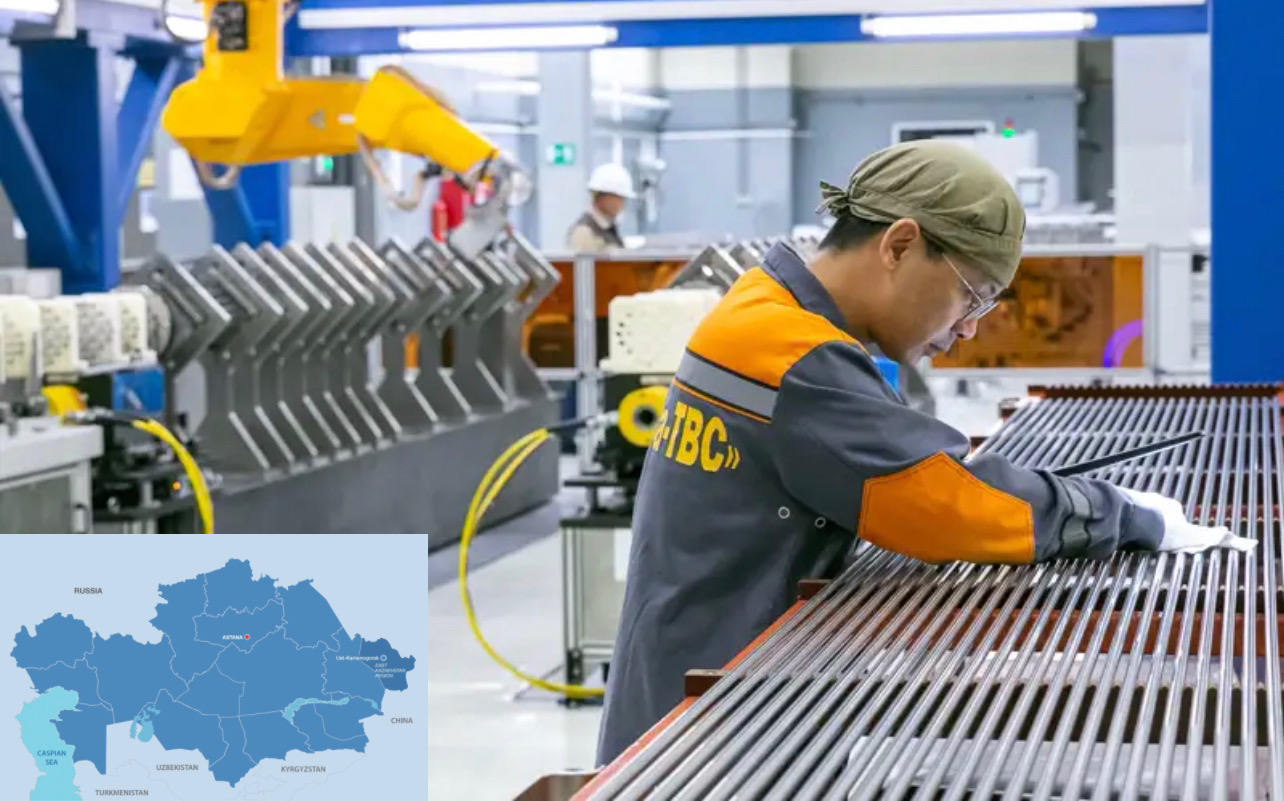
Photo credit: Soltan Zheksenbekov/Kazinform. Click to see the map in full size. The map is designed by The Astana Times.
A potential answer lies in Oskemen, home to the Ulba Metallurgical Plant (UMP). Kazinform agency recently visited this unique facility in Central Asia to learn more about its operations.
Unique asset
Founded in October 1949, the Ulba Metallurgical Plant (UMP) has established itself as one of the world’s leading manufacturers of uranium, beryllium, tantalum, and niobium products. It caters to the needs of nuclear energy, electronics, metallurgy, and other industries. Since 1997, UMP has been part of the Kazatomprom national atomic company, representing Kazakhstan’s interests in the nuclear industry.
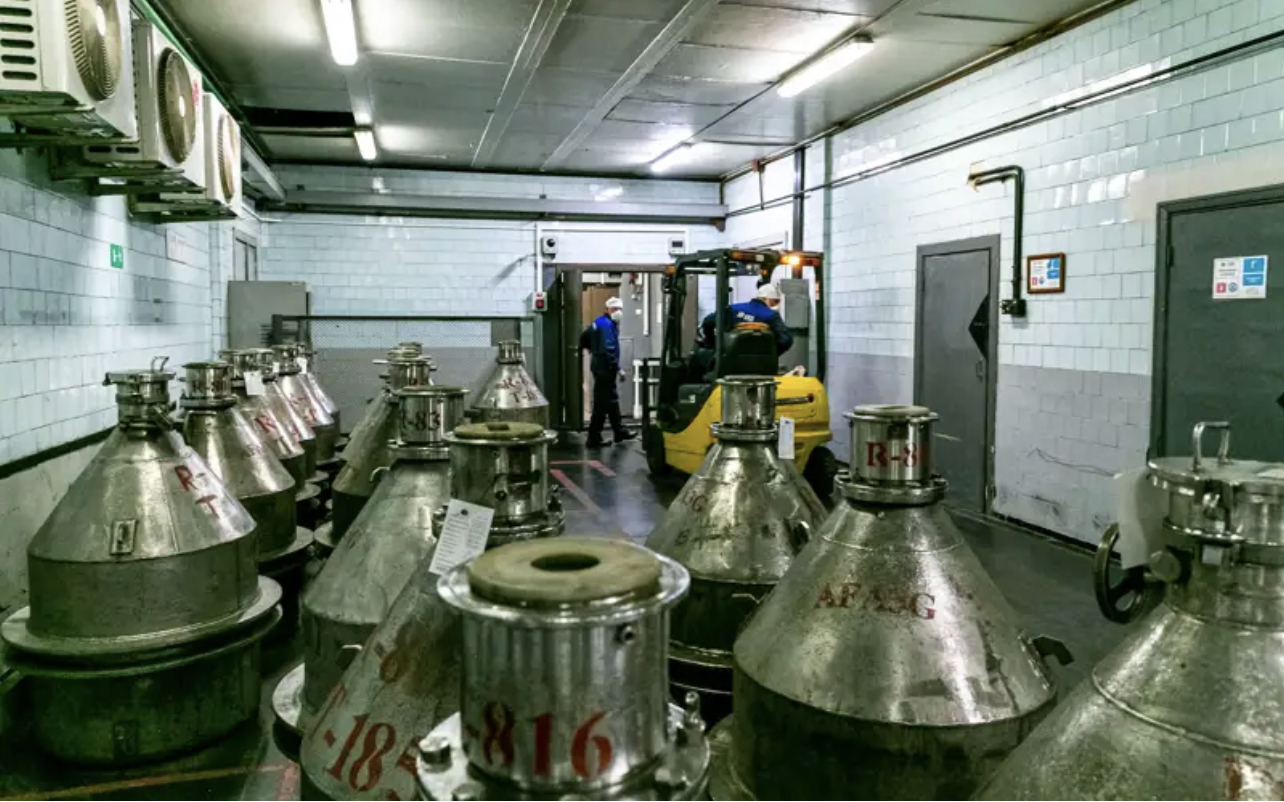
A fuel assembly is a specialized engineering product designed to generate thermal energy in a nuclear reactor. Photo credit: Soltan Zheksenbekov/Kazinform
At the Ulba-TVS plant, a facility within UMP, uranium fuel components for nuclear power plants are produced. According to Yulia Antonova, head of the company’s public relations department, the Ulba-TVS plant is a joint Kazakh-Chinese venture, with 51% of shares owned by UMP and 49% by China’s CGNPC-URC.
“The plant is unique in that it is the only enterprise in Kazakhstan and Central Asia that produces fuel for nuclear power plants. The design production capacity is 200 tons of low-enriched uranium per year, equivalent to about 440 fuel assemblies annually. In 2024, it is planned to reach full design capacity. Equipment manufactured in France, Germany, the USA, China, and Kazakhstan is installed here,” Antonova explained.
What is a fuel assembly?
A fuel assembly is a specialized engineering product designed to generate thermal energy in a nuclear reactor. Inside the assembly, fuel pellets made of uranium are placed, which play a crucial role in the nuclear energy generation process.
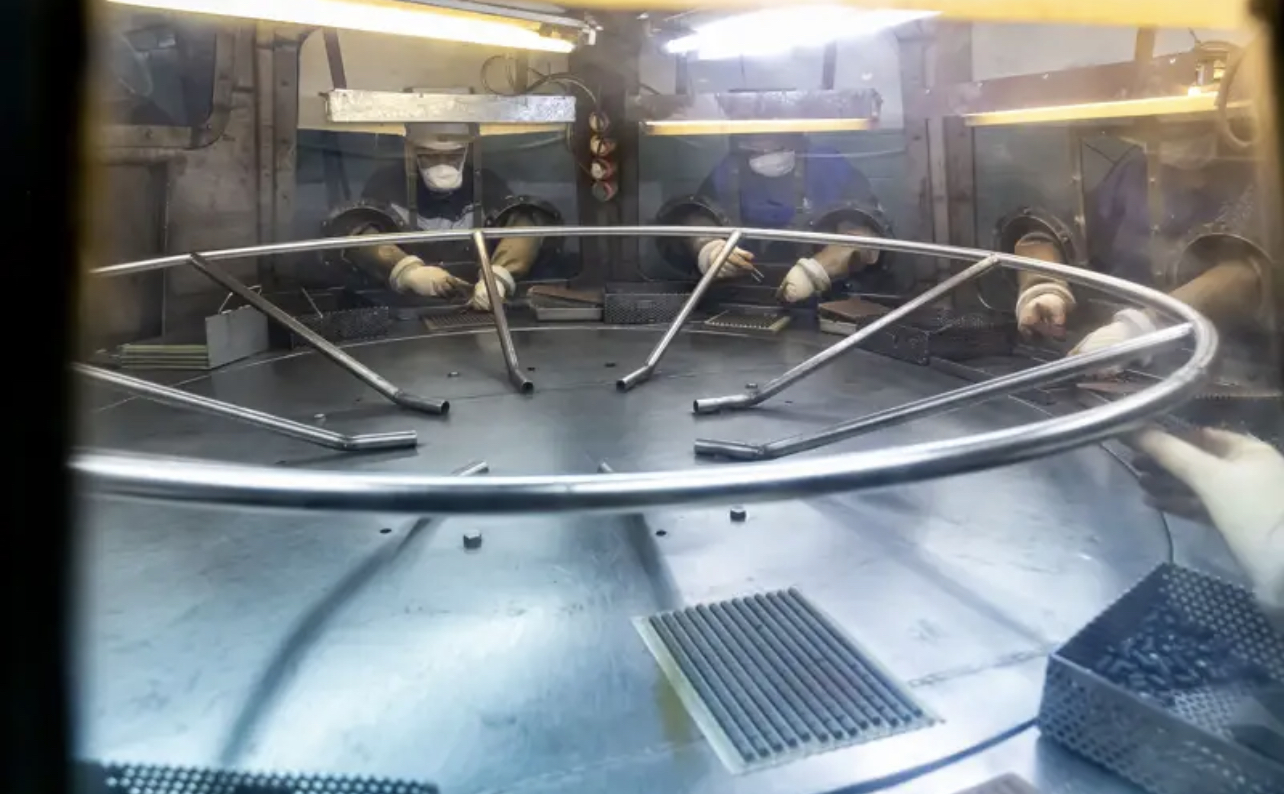
The production of a fuel assembly begins with natural uranium mined in Kazakhstan. Photo credit: Soltan Zheksenbekov/Kazinform
The production of a fuel assembly begins with natural uranium mined in Kazakhstan. However, before it can be used as nuclear fuel, natural uranium must be converted into hexafluoride (UHF) and enriched in the isotope 235, usually to less than 5%. This process involves sending natural uranium to Russia for conversion and enrichment. The enriched uranium is then delivered to UMP to produce powders and fuel pellets.
How are fuel assemblies made?
The journey from uranium to fuel pellets is meticulous at the UMP. Acting Head of the Uranium Production Shop Vladislav Kogai described the steps involved.
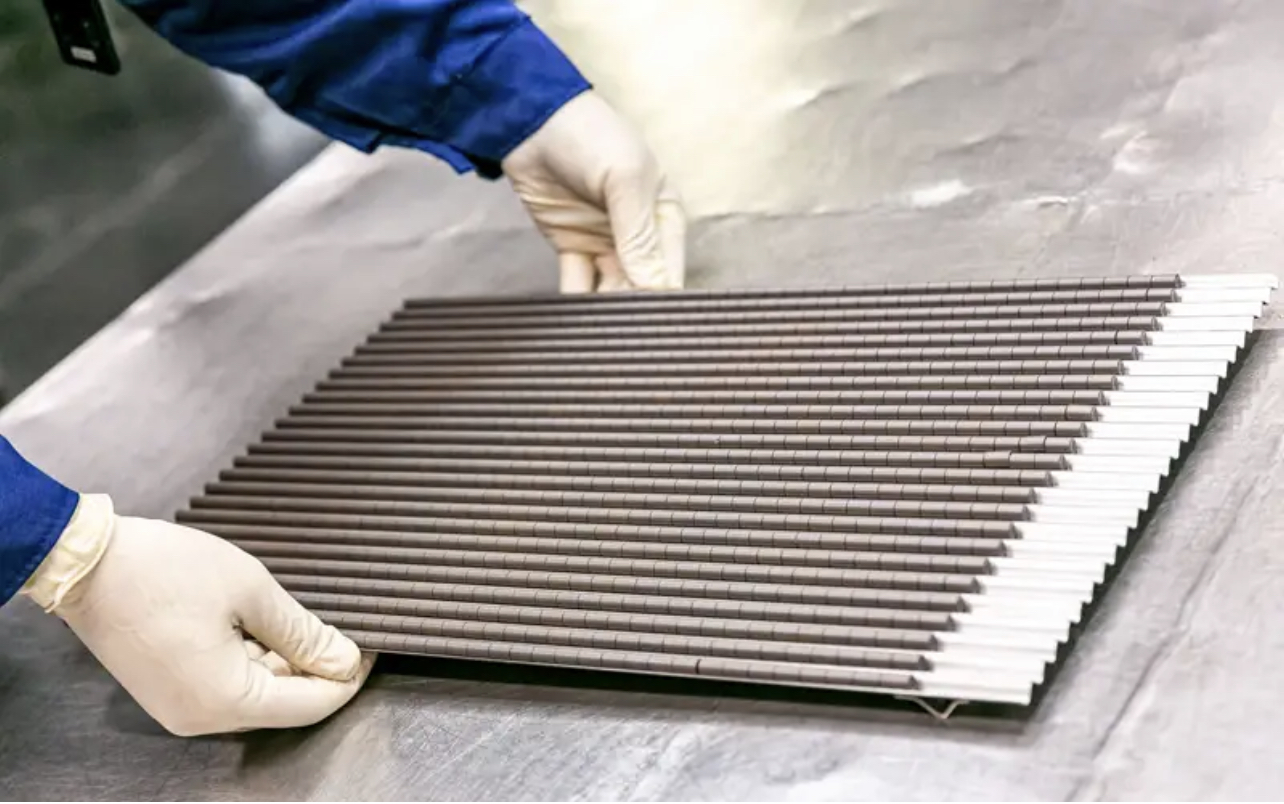
The plant operates continuously, with employees working in three shifts to ensure uninterrupted production. Photo credit: Soltan Zheksenbekov/Kazinform
“First, we add a dry porous agent to the uranium. This is followed by the molding and sintering process. Then, the pellets are ground and inspected for defects. The entire process, from powder to finished pellet, takes about 12 days,” Kogai said.
The plant operates continuously, with employees working three shifts to ensure uninterrupted production.
How are fuel assemblies transported?
The fuel pellets are transported for export and assembled into fuel assemblies. This process occurs on a dedicated fuel assembly line that includes a lifting platform, an assembly rotary platform, and a table for pulling fuel rods.
Fuel rods are created using advanced technology. The cladding tubes are manually placed on a buffer table before being automatically moved along the transport line. The operator monitors the process, ensuring that any deviations are addressed promptly. After stages such as purging, purity control, welding, and visual inspection, the tubes are filled with pellets using a vibration loader.
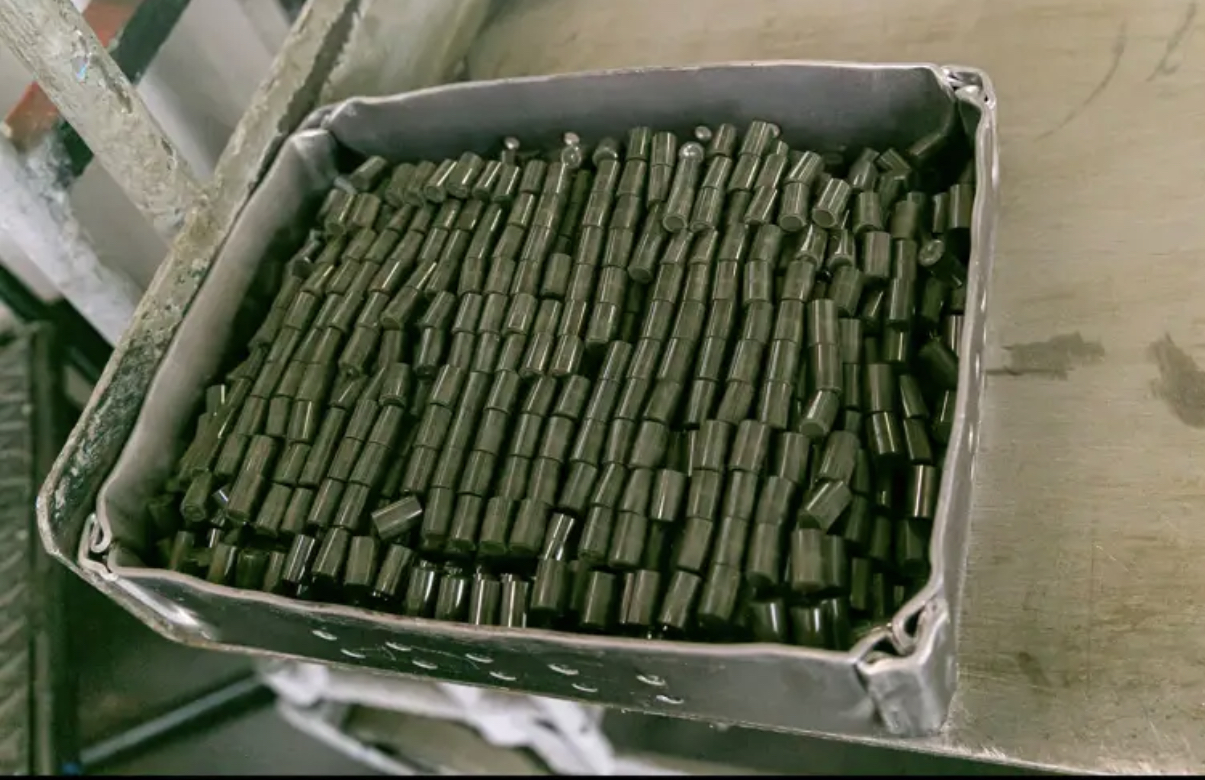
Each fuel assembly stores 450 kg of uranium, and the plant’s design capacity allows for producing 440 fuel assemblies annually. Photo credit: Soltan Zheksenbekov/Kazinform
The process does not end there. The fuel elements are then attached to a skeleton—a tetrahedral frame made of tubes and gratings that form the structure of the fuel assembly. A special robotized machine welds this assembly and checks for precision using a coordinate measuring machine.
Each fuel assembly stores 450 kg of uranium, and the plant’s design capacity allows for producing 440 fuel assemblies annually. Under strict control, these finished products are exported to China by rail, thanks to the partnership with CGNPC-URC. In the last few years, five shipments of fuel assemblies (up to 150 tons of low-enriched uranium) were made to Chinese nuclear power plants. As of July 2024, eight deliveries had been completed, or 240 tons of low-enriched uranium.
The International Atomic Energy Agency (IAEA) frequently inspects the plant. Since its founding, the UMP has had a flawless safety record, with no emergency situations reported so far.
The IAEA’s Low Enriched Uranium Bank
The UMP is also home to the Low Enriched Uranium (LEU) Bank, a reserve of low-enriched uranium in the form of uranium hexafluoride (UF6) controlled by the IAEA. The LEU Bank is a guaranteed reserve for IAEA member states in case of supply interruptions.
The LEU Bank officially started operations in December 2019, with a current volume of 90 tons of low-enriched uranium. The reserve has yet to be utilized, highlighting the robustness of the global nuclear fuel supply chain.